Tauko - from design to finished product
Zofia has been working for Nowy Styl for 15 years now. At the moment she’s our Portfolio Manager, but when she started, she was assigned to a different area. For the first 7 years she worked for the Marketing Department. This is where her love for chairs started. Zosia used to develop marketing strategies for various lines of chairs, until one day she was offered the opportunity to pursue a career path in the Product Management Department.
Marcin has been with Nowy Styl for 27 years - since the very beginning. First he worked at the production, and then at the sewing shop, where he soon became a master - this is how we refer to production team leaders. Then, after about 10 years he joined the newly created Technology Department. The cutting room is a dozen metres away from the technology office, so it was not a far journey. Nowadays Marcin is the head of the whole implementation section.
Marcin has been with Nowy Styl for 27 years - since the very beginning. First he worked at the production, and then at the sewing shop, where he soon became a master - this is how we refer to production team leaders. Then, after about 10 years he joined the newly created Technology Department. The cutting room is a dozen metres away from the technology office, so it was not a far journey. Nowadays Marcin is the head of the whole implementation section.
Zofia and Marcin will tell us a few words about what their work looks like in practice. Explore the story behind the Tauko chair, told by those who saw its origins.
-
Zofia
-
Marcin
Tauko – home comfort in the office
In one of the meetings of the Product Management Department in 2014 we had an idea to come up with a new office chair, whose design and profile would be a reference to home interiors. The main assumption was to combine soft upholstery with wood and plywood. The product line also included modular conference tables and hockers.
When working on this project, we wanted to draw on our experience in woodworking. We have our own woodworking plant, where we make beech plywood and solid wood elements. That's how we came up with the idea of a chair whose characteristic feature would include bent plywood.
Zofia
Portfolio Manager
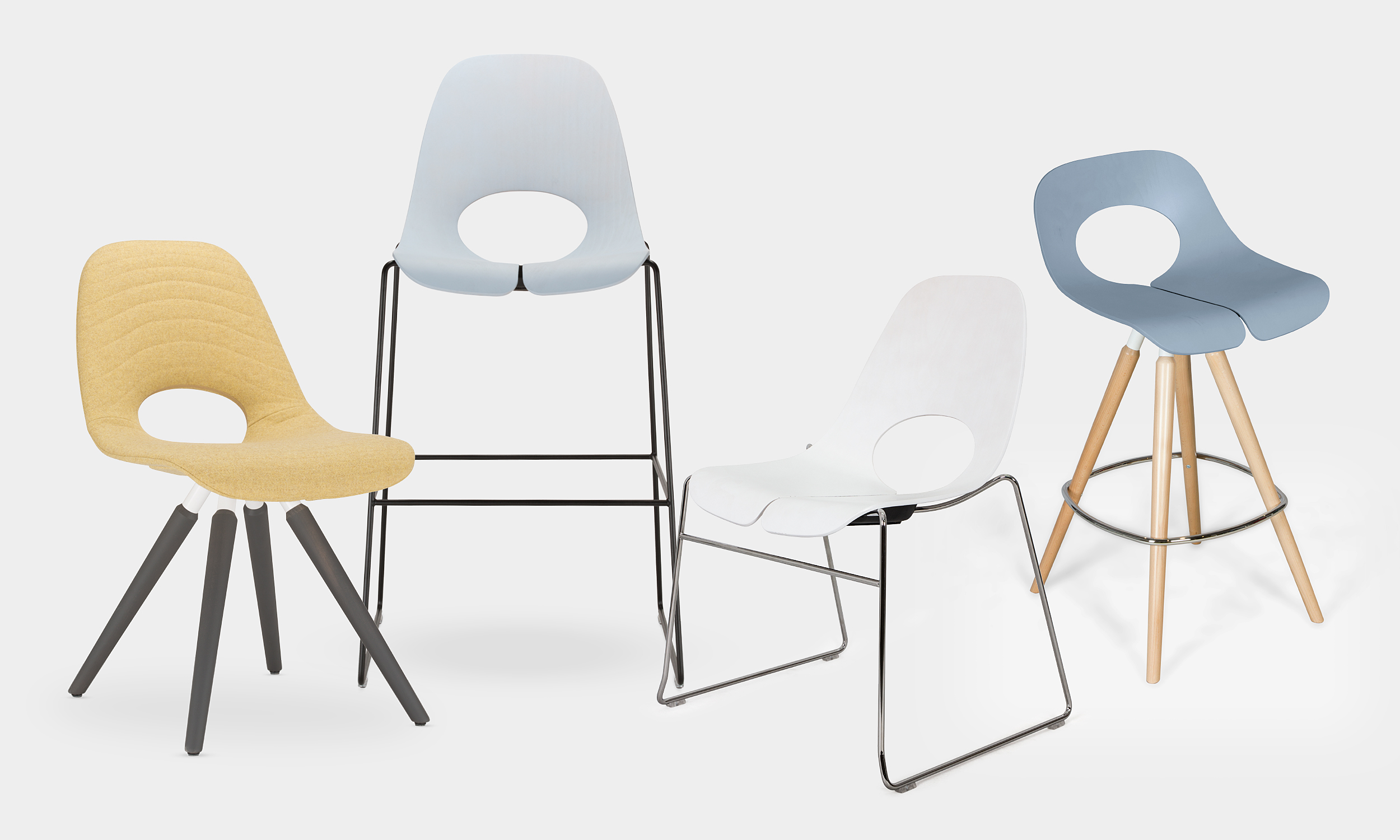
Design
We wondered how the designers would understand the needs we outlined in the brief. We were curious how they would respond and wanted to see if we share any of the notions.
The design by Mac Stopa stood out against the others and immediately drew our attention – it offered something new and fresh. It was something we never saw in our portfolio before. The design was a reference to the Shell chair by Teresa Kruszewska (1956) and to the Medea chair by Vittorio Nobili (1955). Both of these designs were never included in mass production, though. "Shell Chair" designed by Teresa Kruszewska Photo: National Museum in Warsaw
"Shell Chair" designed by Teresa Kruszewska
"Shell Chair" designed by Teresa Kruszewska
Photo: National Museum in Warsaw
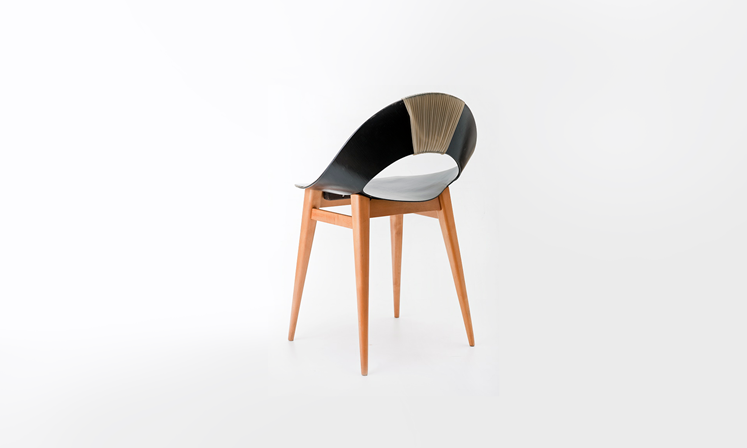
What was it then that made the Tauko design by Mac Stopa different? Why are thousands of these chairs used in various European countries?
A road not without bumps
When we started to work on this chair, it turned out that the design by Stopa cannot be wholly implemented in its original shape, because plywood would break when we tried to bend it with standard methods. That’s when the designer proposed another approach. Since he had experience working with this material, he came up with a new way of bending plywood sheets – rather than use a single flat sheet we put together two “wings” of the seat.
The problem with the original model was that the more we arched the backrest to make it wrap around human back, the more the upper curve had to be flattened, which meant the sharp top edge hurt the user’s back. The same was true of the seat – as we elevated the sides, we had to flatten the front, making it uncomfortable to sit on. Plus, the traditional bending method made the opening in the upper part of the bucket seat very small.
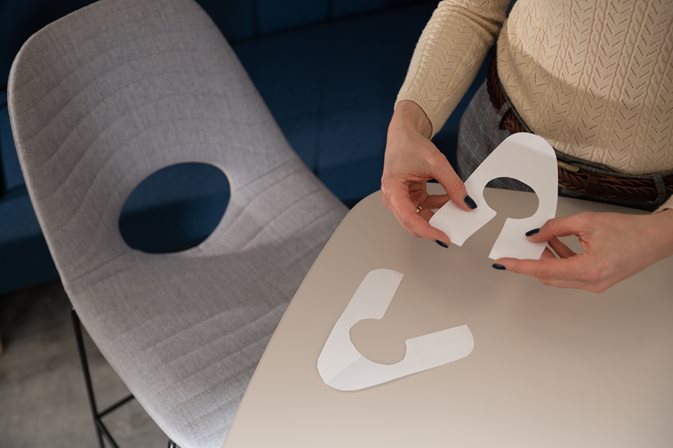
Together with Mac Stopa we thought of a new way, which eliminated all of these issues and made it possible to tilt the backrest to make the Tauko seat comfortable even if you choose to spend a few hours in it.
Zofia
Portfolio Manager
Expanding the line
Only a few selected versions were forwarded to the production stage. We chose the models that were best suited to office zones and could contribute some cosy, homely atmosphere to any workspace. Tauko chairs and modular tables are a good alternative to uncomfortable chairs and traditional seminar tables. Their modular construction, optimum tabletop size and easy assembly mean each participant of a training or meeting has their own single table, which can be joined to others or separated at will.
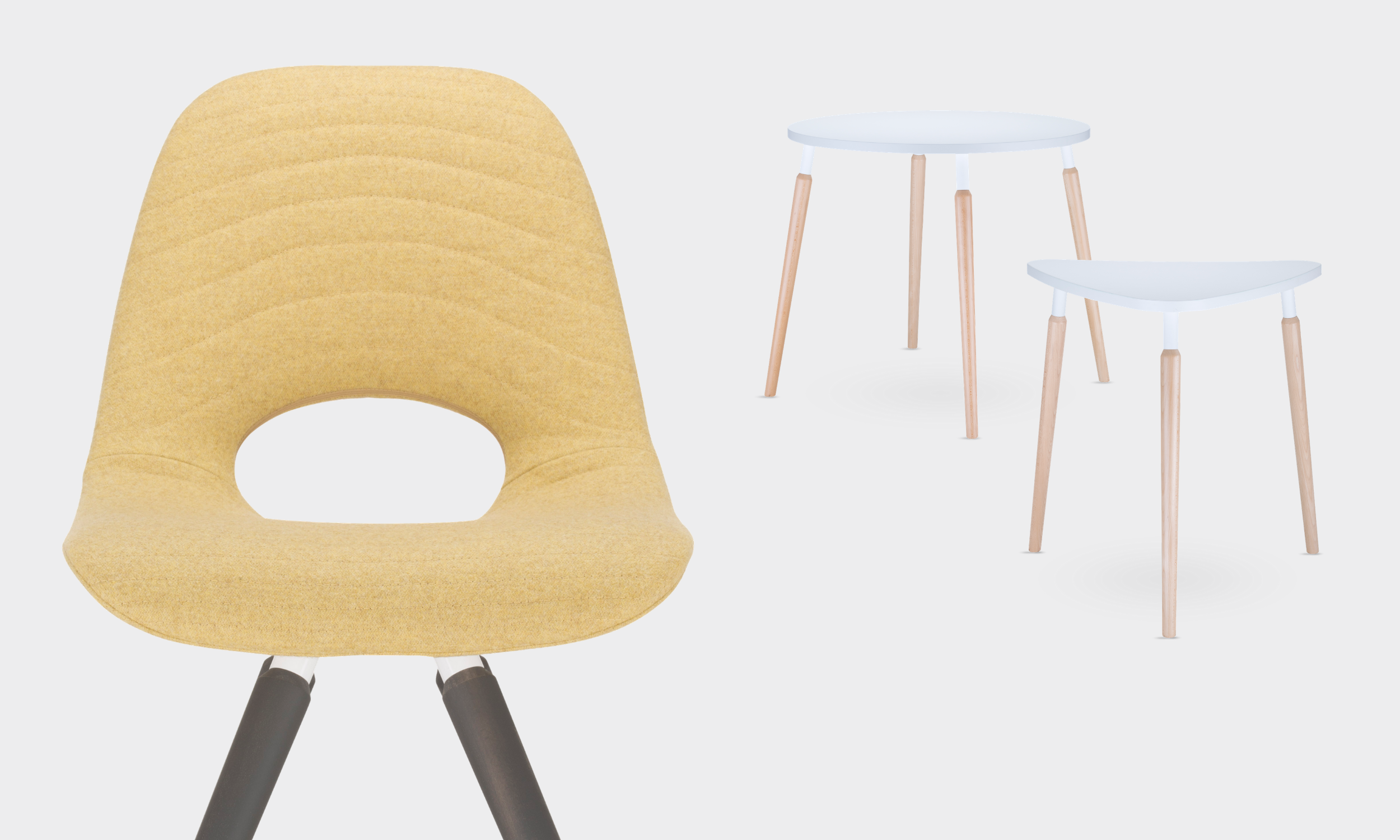
Engineering aspects
The Implementation Section at Nowy Styl is a team of experienced engineers who have been with us for years. Their everyday efforts are focused on supervising the production process, starting from the prototype to the model that is approved for production. But before a piece of furniture can actually be sold, the whole section oversees the entire technological process. Their meticulous calculations are used to define the time needed to cut, sew and assemble the upholstery. The engineers know how many metres of fabric should be used, how much foam filling goes into the seat and how many staples will reinforce the finished upholstery – they keep track of the demand to make sure all the materials are there to use.
The engineers work in the office, in front of their PC screens, in a familiar-looking open space setting. But they spend only half of their total working time there. The other half is prototyping and making models – that’s when they are busy cutting, assembling, sewing and upholstering. This means every engineer knows the basics of sewing. No need to say, this is a useful skill you can fall back on in your private life, too! Marcin admits he sometimes does some minor sewing at home, too. – Sewing is like driving a car – if you do it every day, it becomes automatic. But when you stop for a while, it starts to be a problem – says Marcin. That’s why at work he leaves sewing to experts. The same is true of upholstering. A lay person won’t recognize a prototype sewn and upholstered by an engineer, but we know the difference. Our specialists pay immense attention to detail and their work is highly accurate and attractive.
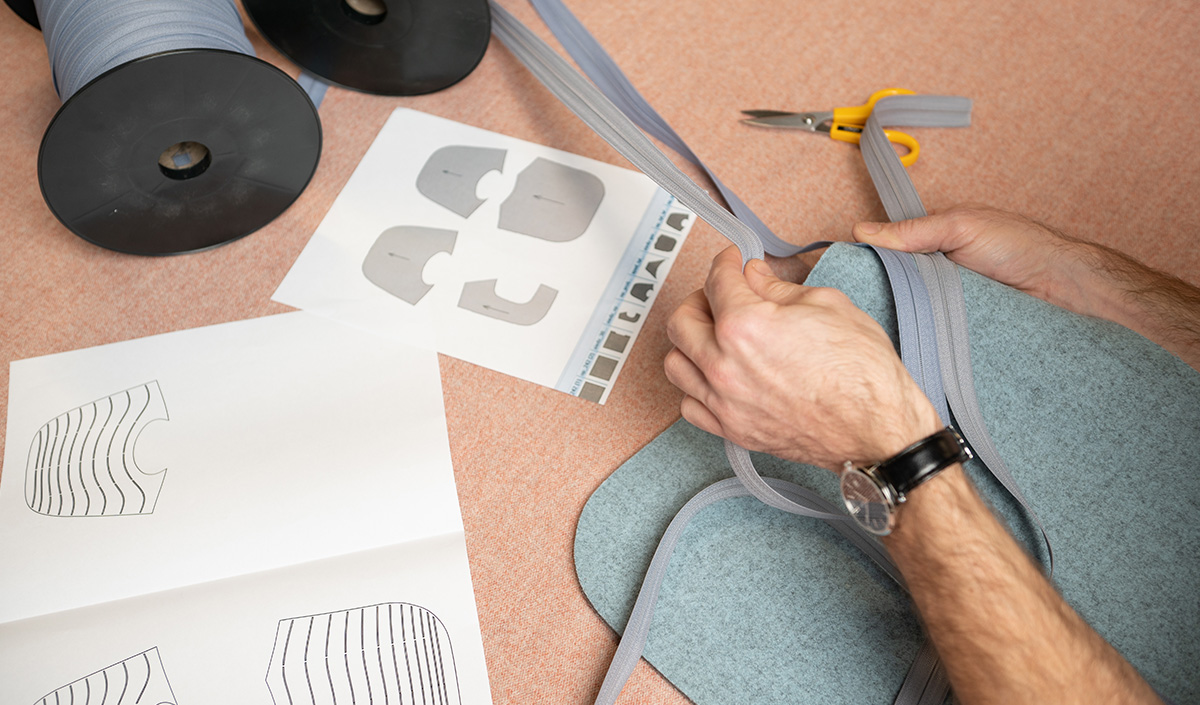
Project manager, product manager, constructor and engineer - this team works together from the very beginning. They start with the design. Using the design prepared by Mac Stopa, our designers, together with implementation technologists from a wood processing company, have developed the shape of the Tauko bucket seat and prepared the wooden frame. Then they designed what materials should be used for the seat and backrest, and then they designed the shape of upholstery to be used on the prototype.
The foam filling comes in different thickness and hardness. It’s our job to find the perfect compromise between comfort, design and cost. The engineer’s work at this stage is a lot like a tailor’s job. First you take the measurements, then you only tack the clothes and then you ask the customer to try them on. The same goes for a chair – first you sew the model, then you adjust it and after a lesson learnt you introduce the adjustments. The first attempt is never perfect and you always need to amend something
Marcin
Technology Department
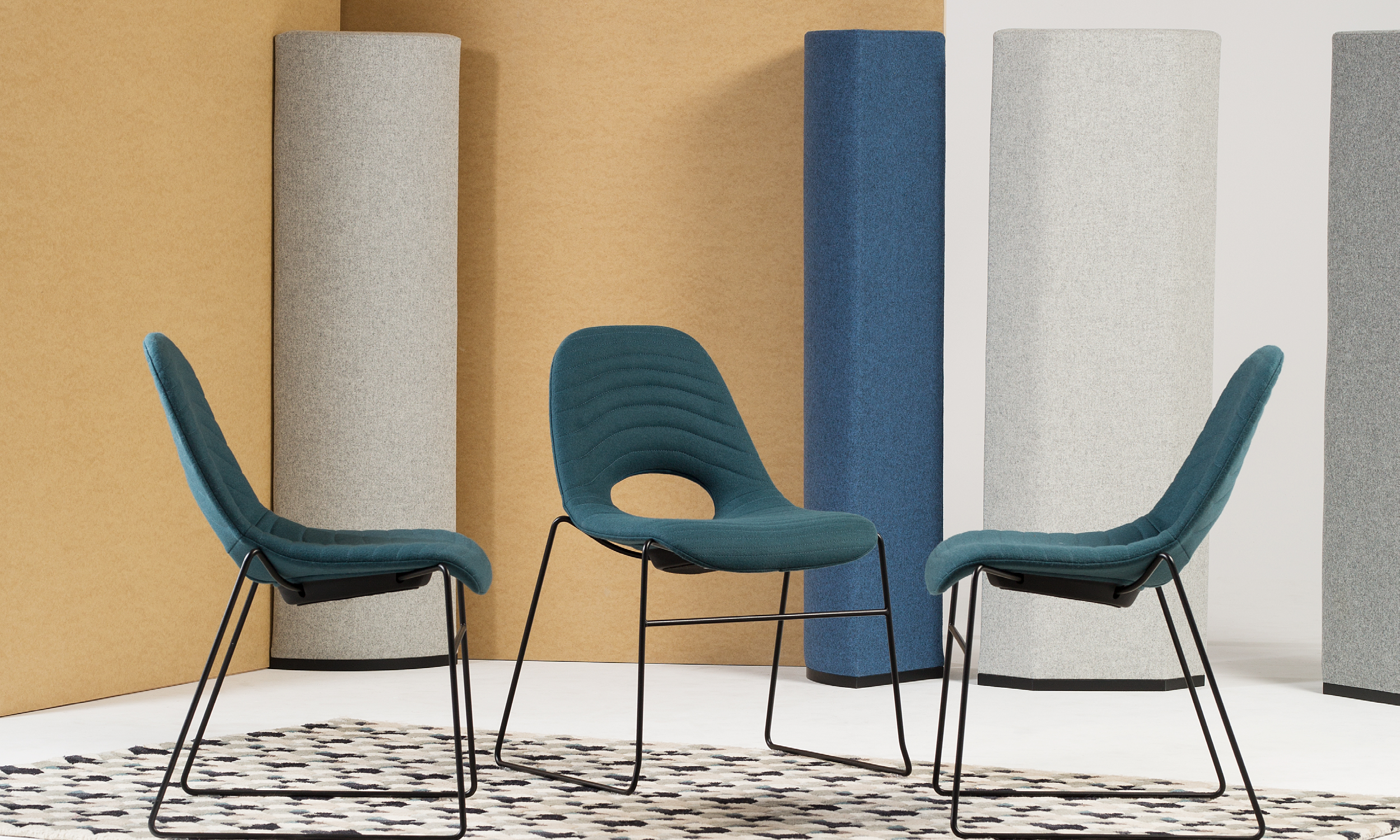
After the first stage is over, you come up with another prototype and you continue until you’re happy with the results. It can take a dozen trials or so, especially when the shape is complicated. In order to make sure that the waves on the backrest are the same, so that each chair is identical, special steel templates were prepared with laser-cut openings. The seamstresses first draw the lines using the template, and then do the stitching.
We already have a large stock of upholstery fabric. We could make a piece that would cover the whole National Stadium or the highway from Kraków to Katowice!
Marcin
Technology Department
The last stage is making the final prototype. If it’s approved, we can continue with implementation. This is when the engineer prepared process sheets, a list of operations to be completed (with specific timing), and job instructions (gluing, sewing, upholstering etc.). At this stage the engineer also calculates the standard amount of individual materials necessary to make a single chair. The fabrics often vary in reel width, pattern and stretch. We also check the packaging and once the chair is ready, it’s tested for stability and certified.
A few dozen people are involved in launching a single production line. First a pilot series is planned and if all goes well, the chair is launched in regular production.
– The engineer is still responsible for a product when it’s in the growth stage. We check whether the employees of each production shift know how to make a specific model. An engineer is a caregiver, supervisor and personal coach - all in one – adds Marcin with a smile.
A few dozen people are involved in launching a single production line. First a pilot series is planned and if all goes well, the chair is launched in regular production.
– The engineer is still responsible for a product when it’s in the growth stage. We check whether the employees of each production shift know how to make a specific model. An engineer is a caregiver, supervisor and personal coach - all in one – adds Marcin with a smile.